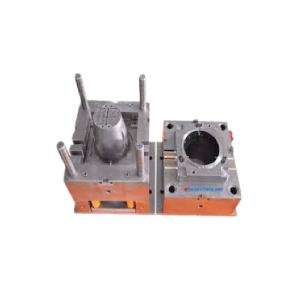
Add to Cart
Plastic Injection Mold Custom Plastic Parts Manufacturer
Plastic Injection Molds Description:
The temperature of each point of the injection mold is not uniform, which is also related to the time point of the injection molding cycle. The function of the mold temperature machine is to keep the temperature constant between 2min and 2max, that is, to prevent the temperature difference in the production process or in the gap from fluctuating up and down. The following control methods are suitable for controlling mold temperature: Controlling fluid temperature is the most common method, and the control accuracy can meet the requirements of most situations. With this control method, the temperature displayed by the controller is inconsistent with the mold temperature; since the thermal factors affecting the mold are not directly measured and compensated, the mold temperature fluctuates greatly. These factors include changes in the injection cycle, injection speed, melt temperature and room temperature. The second is to directly control the mold temperature. This method is to install a temperature sensor inside the mold, which is only used when the mold temperature control accuracy is relatively high. The main features of mold temperature control include: the temperature set by the controller is consistent with the mold temperature; the thermal factors affecting the mold can be directly measured and compensated. In general, the stability of the mold temperature is better than by controlling the fluid temperature. In addition, mold temperature control has better repeatability in production process control. The third is joint control. Combination control is a combination of the above methods while controlling the temperature of the fluid and the mold. In joint control, the location of the temperature sensor in the mold is extremely important. When placing the temperature sensor, the shape, structure and location of the cooling channel must be considered. In addition, the temperature sensor should be placed in a position that determines the quality of the injection molded part. There are many ways to connect one or more mold controllers to an injection molding machine controller. From the point of view of operability, reliability and interference immunity, it is better to use a digital interface.
Plastic Injection Molds Parameter:
Keywords | Plastic Injection Molds |
Brand Name | OEM/ODM |
Model Number | OEM |
Shaping Mode | Plastic Injection Mould |
Product Material | Plastic |
Description | Plastic Injection Mould |
Lead Time | 30 Days |
Size | Customized |
Application | Industry Plastic Parts |
Color | Customized |
Place Of Origin | China |
Plastic Injection Molds Factory Introduction:
Huishuo Co., Ltd. is located in Dongguan City, China, and has been committed to the design and manufacture of precision metal stamping dies and injection molds since 2009, including metal stamping and injection molding. In terms of progressive stamping dies, our products mainly involve precision terminals, connectors, contacts, clips, shrapnel, shells, shielding covers, etc. In metal stamping, there are many precision presses with tonnage ranging from 25T-160T, all of which are gantry high-speed machines. It can produce various coils and strips with a degree of 0.05-4.0mm. The stamping materials include cold rolled steel, stainless steel, phosphor bronze, brass, red copper, beryllium copper, lead frame materials, etc. Regarding plastic injection molding production, we have many injection molding machines of various types between 50-160T, focusing on the production and processing of various plastic products.